An Introduction to EcoPacesetter
Eco Pacesetter LLC is proud to announce the introduction of the Eco Pacemaker System which has been developed over 12 years of research and extensive field testing on virtually every type of large industrial equipment in the industry.
The Pacemaker System has been lab tested for emissions reduction and soot dyno analysis in “real-time”, alongside comprehensive in-house testing at Eco Pacesetter LLC for our own due diligence in confirming the success of this product.
The Pacemaker System uses the same principle as catalytic converters with the remarkable oxidative properties of platinum, but at the beginning of the energy process rather than at the end, instead turning what fuel would usually be ejected as harmful engine emissions into usable energy for the engine. An overview of how our injector system and catalyst works is in a later section.
This system reduces harmful emissions, improves an engine’s efficiency, increases torque to an engine, and reduces fuel usage by an average of 10% all by catalyzing the combustion reaction to burn more fuel than normally possible without other specialized systems that come with their own complications.
Who Benefits from Our System & Catalyst?
Our patent-pending Pacemaker Injector System & Catalyst have been tested on a multitude of large diesel engines, all yielding incredible results with an average 10% on fuel savings, a 60%-90% reduction of the opacity of exhaust fumes (see image below), and variable savings on engine maintenance based on the model and age of said engine.
However, our system and catalyst are not suitable for smaller consumer scale engines due to the initial cost of the Pacemaker system and the recurring cost of the catalyst outweighing the benefits a smaller engine would gain. This can be shown on this website’s built-in excel calculator for determining your approximate savings from purchasing our Pacemaker system and Catalyst.
Suffice to say, any piece of diesel equipment that runs more than 8 gallons/hour will not only see an average of 10% in fuel savings, but a reduction in maintenance costs as well.
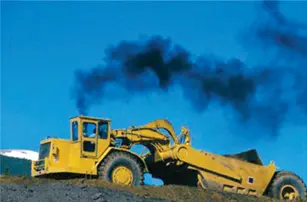
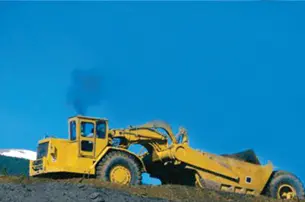
The Problem Our Products Solve and How They Do It!
First, what is the problem that our system solves? 3 factors in the combustion process prevent an approximate 20% of the aerosolized fuel from combusting and being converted into energy alongside drops in engine efficiency over time:
- Nitrogen makes up 70% of the air content, so during combustion it reacts with some of the oxygen to form oxides of nitrogen (NOx), which are another form of harmful emission and take away the oxygen content that could combust with fuel hydrocarbons.
- Some systems have been designed to run on oxygen rich combustion cycles, but those systems come with other complications such as higher chamber pressures and high temperature gaseous oxygen in exchange for removing the carbon build-up and emission issues.
- With the air to fuel mixture in the combustion chamber not being completely homogeneous, meaning uniform, pockets of higher concentrations of either fuel or air can form, meaning not all the fuel is exposed to oxygen to combust during the cycle.
- Due to the incomplete combustion of hydrocarbons, especially in a fuel-rich combustion, carbon formation (also known as coking), causes carbon build-up within the engine which causes drops in performance and can damage components faster than through normal wear & tear.
Our approach to solving this problem takes inspiration from the process used by catalytic converters, but at the beginning of the combustion process rather than at the end. Using the amazing oxidative properties of platinum alongside other additives, our catalyst improves the rate of combustion to utilize an average of 10% more fuel during combustion, cleans existing carbon build-up in the engine to improve performance retroactively, and reduces the amount of harmful emissions like oxides of nitrogen (NOx) and un-combusted hydrocarbons being exhausted.
Detailed Savings Analysis
Testing data for our patent-pending Pacemaker Injector System and Catalyst shows an average 10% on fuel savings through a mixture of removing carbon build-up that lowers efficiency, increasing the amount of fuel burned in the combustion stage, and overall improving the mechanical health of the engine.
Further savings are difficult to calculate due to variability, but with the catalyst cleaning the engine of carbon build-up and using more of the atomized fuel during combustion, there is a reported increase in torque (getting the same power out of less fuel); maintenance isn’t required as often; operating time is increased due to not requiring fuel-ups as often; fewer oil changes are required; and fuel injector failures don’t happen as often.
A few savings examples can be found below. All the calculations below are for a single piece of equipment and show that this system is the most useful for fuel savings on diesel equipment with higher fuel consumption rates. However, other savings can be accomplished through the general improvement of the engine’s health by the removal of carbon build-up to reduce maintenance expenses and increase engine longevity.
For the sake of calculation, the following assumptions on the work-conditions and engine uptime will be made, with the expenses/savings approximations below only applying under this context as the final numbers can change based on variations in the work-conditions and engine uptimes.
- Weekly engine uptime is an average of 40 hours/week.
- The equipment is in-use 52 weeks/year at the above engine uptime hours.
- Average fuel costs for the year are $3.00
At present, Freightliner is the most popular Semi-Truck manufacturer with a 40% market share selling 96,792 class 8 trucks for this year, with the Cascadia model being their most popular model over the years. However, for previous generations that most frequently have a fuel economy range of 6-8mpg, which translates to 8.5 gallons/hour if they travel at an average 60 miles/hour. So, our Pacemaker Injector System and Catalyst are cost-effective fuel savings wise for older model trucks with lower fuel economies.
Taking that 8.5 gallons/hour and using the assumptions above on work conditions & engine uptime, that would be 17,680 gallons of fuel for the year and $53,040 in fuel expenses. With the average 10% fuel savings our System & Catalyst provide and accounting for the initial cost of our Pacemaker Injector System and recurring cost of catalyst refills, the first year you would break even and save $2,828.8 every following year under those precise conditions.
For the sake of calculation, the following assumptions on the work-conditions and engine uptime will be made, with the expenses/savings approximations below only applying under this context as the final numbers can change based on variations in the work-conditions and engine uptimes.
- Weekly engine uptime is an average of 40 hours/week.
- The equipment is in-use 52 weeks/year at the above engine uptime hours.
- Average fuel costs for the year are $3.00
Commercial Farming Tractors can consume anywhere between 5 gallons/hour to 20 gallons/hour, or even more. So, for this example let's use an average fuel consumption rate of 12.5 gallons/hour and use the assumptions mentioned above on work conditions.
- For more precise fuel consumption rates, reference your tractors owner manual as many commercial tractor manufacturers include such data for the specific model tractor under various workloads and conditions.
Under the above assumptions on work-conditions and engine uptime alongside the 12.5 gallons/hour average, the yearly expenses for that piece of equipment would be $78,000 in fuel alone. With the average 10% fuel savings our Pacemaker System and Catalyst provide, accounting for the initial cost of our system and recurring cost of catalyst refills, the first year you would save $1,397.50 and save $4,160 every following year under those precise conditions.
For the sake of calculation, the following assumptions on the work-conditions and engine uptime will be made, with the expenses/savings approximations below only applying under this context as the final numbers can change based on variations in the work-conditions and engine uptimes.
- Weekly engine uptime is an average of 40 hours/week.
- The equipment is in-use 52 weeks/year at the above engine uptime hours.
- Average fuel costs for the year are $3.00
At the bottom of this drop-down is a table of data on the fuel-usage rates for Caterpillar Brand Bulldozers, collected directly from Caterpillar's performance Handbook for your reference when using the built in approximate savings calculator below this section. The Models in the table below start with the D8 Series of Caterpillar Bulldozer due to the fuel usage of those models being on the lower end of engines our system and catalyst are cost-effective on, up until the D11 series of Bulldozers.
Taking the D8R model dozer and averaging its fuel consumption rates to 11 gallons/hour (averaged between medium & high workloads) and using the assumptions above on work-conditions and engine uptime, the fuel expenses for that single piece of equipment would be $68,640 over the course of a year. With the average 10% fuel savings our System & Catalyst provide and accounting for the initial cost of our Pacemaker Injector System and recurring cost of catalyst refills, the first year you would save $898.30 and save $3,660.80 every following year under those precises conditions.
Now, looking at Caterpillar's largest available Dozer the D11 series, and averaging its fuel consumption rates to 29.6 gallons/hour (averaged between medium & high workloads) you can see that the fuel expenses for that single piece of equipment would be $184,704 per year under the assumed work-conditions and engine uptime. With the average 10% fuel savings our System & Catalyst provide and accounting for the initial cost of our Pacemaker Injector System and recurring cost of catalyst refills, the first year you would save $7,088.38 and save $9,850.88 every following year under those precises conditions.
Caterpillar
Dozer Model
|
Gallons/Hour
(Medium Workload)
|
Gallons/Hour
(High Workload)
|
D8R
|
8.5-11.0
|
11.0-13.5
|
D8T3 |
8.9-11.5
|
11.6-14.2
|
D8T1 |
9.1-11.7
|
11.7-14.3
|
D9T3 |
11.4-14.9
|
14.9-18.3
|
D9T4 |
10.6-13.9
|
13.9-17.0
|
D9T1 |
11.7-15.3
|
15.3-18.9
|
D10T26 |
14.9-19.4
|
19.4-23.9
|
D10T25 |
16.3-21.1
|
21.1-26.0
|
D11T6 |
22.5-29.3
|
29.3-36.0
|
D11T5 |
22.8-29.6
| 29.6-36.4 |
Medium Workload: Production dozing in clays, sands, gravels. Push loading scrapers, borrow pit ripping, most land clearing applications. Medium impact conditions. Production landfill work.
High Workload: Heavy rock ripping. Push loading and dozing in hard rock. Working on rock surfaces. Continuous high impact conditions
For the sake of calculation, the following assumptions on the work-conditions and engine uptime will be made, with the expenses/savings approximations below only applying under this context as the final numbers can change based on variations in the work-conditions and engine uptimes.
- Weekly engine uptime is an average of 40 hours/week.
- The equipment is in-use 52 weeks/year at the above engine uptime hours.
- Average fuel costs for the year are $3.00
At the bottom of this drop-down is a table of data on the fuel-usage rates for Caterpillar Brand Bulldozers, collected directly from Caterpillar's performance Handbook for your reference when using the built in approximate savings calculator below this section. The Models in the table below start with the 986H Model of Caterpillar Loader due to the fuel usage of those models being on the lower end of engines our system and catalyst are cost-effective on, up until the 994H Model of Loader.
Similar to the analysis example #3, this analysis will look at the lowest end piece of equipment our system is cost-effective on, to the highest end piece of equipment of that type as a comparison.
Looking at the 986H Caterpillar Loader Model and averaging its fuel consumption to 9.45 gallons/hour (averaged between medium and high workloads), and using the same basic assumptions above work-conditions and engine uptime:
- The amount of fuel used for that single piece of equipment in one year would be 19,656 gallons and the fuel expenses for that year would be $58,968.
- If our system was installed on that piece of equipment, the annual amount of fuel saved would be 1,965.6 gallons, the expenses saved for the first year when accounting for initial costs would be $382.46, and every following year you would save $3,144.96.
Now, looking at the 994H Model Caterpillar Loader and averaging its fuel consumption to 42.25 gallons/hour (averaged between medium and high workloads), and using the same basic assumptions above on work-conditions and engine uptime:
- The amount of fuel used for that single piece of equipment in one year would be 88,400 gallons and the fuel expenses for that year would be $265,200.
- If our system was installed on that piece of equipment, the annual amount of fuel saved would be 8,840 gallons, the fuel expenses saved for the first year would be $11,298.30 when accounting for the initial cost of our system, and every following year you would save $14,060.80.
Caterpillar Loader Model
|
Gallons/Hour
(Medium Workload)
|
Gallons/Hour
(High Workload)
|
986H | 7.2-9.5 | 9.5-11.7 |
988H |
10.6-13.9 | 13.9-17.2 |
988K | 9.0-11.8 | 11.8-14.6 |
990H | 15.4-19.8 | 19.8-24.2 |
992K | 20.0-26.0 |
26.0-32.0 |
993K |
23.1-30.3 | 30.3-37.0 |
994H | 32.5-42.4 | 42.4-52.0 |
Medium Workload: Intermittent aggregate truck loading from stockpile, hopper charging or load and carry on firm, smooth surfaces for short distances with minimal grades. Free flowing, low density materials. Light utility, industrial and construction applications. Light snowplowing.
High Workload: Continuous truck loading from stockpile and hopper charging. Loading from bank or load
and carry-on normal surfaces with low to medium rolling resistance and slight adverse
grades. Low to medium density materials in properly sized bucket. Assumes normal travel
distances associated with high productivity stockpile load-out and batch plant applications.
For the sake of calculation, the following assumptions on the work-conditions and engine uptime will be made, with the expenses/savings approximations below only applying under this context as the final numbers can change based on variations in the work-conditions and engine uptimes.
- Weekly engine uptime is an average of 140 hours/week.
- The equipment is in-use 52 weeks/year at the above engine uptime hours.
- Average fuel costs for the year are $3.00
For this example, let's look at a very common freight locomotive series, the EMD SD70 series. There are several models in this series of locomotive, and over 5,700 of them have been produced. On average, a given model in this series that runs at 4000 horsepower burns about 200 gallons/hour under full load and max-throttle conditions.
For this example, the assumptions above will deviate from other examples due to freight trains being run as close to 24/7 as possible for the sake of efficiency and only stopping to refuel, switch out operating crews, and drop-off/pick-up cars. So, to more accurately represent the uptime of such equipment, we'll go with the assumption that a locomotive like one of the EMD SD70 series locomotives run 20 hours/day to account for lull hours, 7 days/week, and 52 weeks/year.
Using the average fuel consumption rate of said engine under full-load and max-throttle conditions at the assumed uptime, the total fuel expenses for the year on that single locomotive would be $4,368,000 for a total fuel usage of 1,456,000 gallons. Accounting for the annual cost of catalyst refills under the specified conditions, annual savings would be $232,960.
Approximate Savings Calculator
Below is a downloadable calculator that you can use to show your projected savings based on the testing data for the Pacemaker Injector System & Catalyst using provided data such as how many systems you intend to buy/use, average engine hours, and average fuel consumption rates.
Listed below is how the calculator is setup for easy use:
- Cells with an orange fill are input cells
- Cells with a green fill are static data points
- Cells with a gray fill and orange text are calculations
Disclaimer: The calculations in this calculator are not exact due to variability in testing found in environmental circumstances, engine build & condition, and measurements data.
Download Link: https://www.ecopacesetter.com/document/share/4/7e0857e1-59dc-48f4-ac22-3a15001c51bf